Yes, before selling gear, you need to build it! It’s easy to buy parts from components suppliers when you want to build a stompbox at home, but when you want to do that at a semi-industrial scale, manufacturing requires professional skills, forces you to make choices, and implies a complex organization.
Every person who has built at least a homemade pedal knows that the mechanical aspects are from far the biggest part of the job: assuming you have some valid schematics, you need to draw some layout for the components on the PCB’s, and you have to stuff that into a box with connectors. You also need to place the switches and pots in such a manner that the device will be easy to use. Then you have to create a decoration that will match your marketing and image objectives.
Some choices, made for the user, can become an issue from an assembly point of view, and vice-versa: some choices, made from a manufacturing point of view, can become an issue for the user. Manufacturing is always a matter of compromise, and the Rockman products are full of these compromises.
When you compare Rockman products with other brands similar items, you can identify five real specific techniques used by SR&D:
- The extensive use of PCB mounting, with a minimum use of panel mounting
- Slider pots and switches, while gear is usually based on rotary pots and switches
- On some devices, all the controls and connections are grouped on the front panel
- Plastic enclosures, which may seem surprising for professional gear
- Last but not least, the half-rack format of the Rockmodules
PCB mounting
In all the Rockman products, everything is fixed on PCB’s: in other terms, the unit is fully operational even if you take the PCB’s out of their enclosures. That’s great for maintenance!
All the jacks and all the pots are PCB mounted, for the best and the worst:
- PCB mounting is much faster to assemble. It’s also a better choice for the audio path, since there is no useless length of wire.
- If the component is both soldered on the PCB and bolted on a panel, there is no mechanical constraint on the PCB. But when a jack is PCB mounted and not bolted, the PCB suffers a lot: after several years, the solder joints break, and the track itself can also break.
The jacks in the Rockmodules are bolted on the rear panel, so the PCB doesn’t support any constraint. In the headphone amps, the jacks are not bolted, and this is a classical issue in old Rockman’s. |
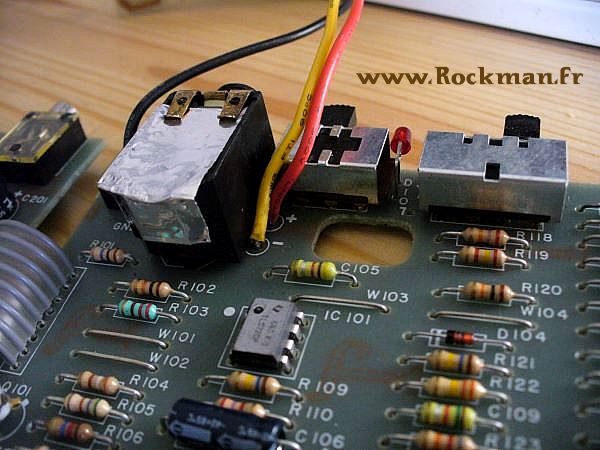 |
Slider pots and switches
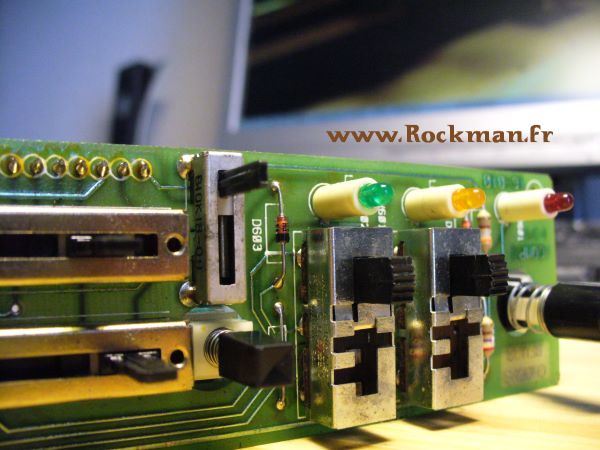 |
If we except the very first SR&D’s item, the Power Soak, rotary controls appeared at SR&D’s only during the last years (AGP and UDG stompboxes, A12-50 combo). All the Rockman products have slider controls (pots and switches), and some push-buttons. They never include rotary controls.
The sliders technique has a lot of advantages:
- Size: mini slider-pots were the only solution to stuff all these controls in half-rack units.
- No knob required: the post and switches used in Rockman gear are handled directly, while rotary pots and switches require panel mounting and a knob.
- Easy assembly: the slider switches and pots are PCB mounted, the front plates are just placed in front of them, with no extra operation needed (no bolting on the front plate).
The push buttons were also PCB mounted, with just a square hole for these tiny knobs (or round hole for the power switches).
|
Front plate concentration
From a user’s point of view, it is logical to have the controls on the front plate, and the connections on the rear plate. But from a manufacturing point of view, it is more efficient to have everything on the front plate.
That’s the reason why the first Power Soak (Model I and Model II) has its input and outputs on the front panel.
The third version, the PS3, had connections on the rear panel, which makes sense for the user, but was a little longer to assemble.
The design of the headphone amps, in 1982, has followed the same principle: all the connections and switches are on the front board, while the enclosure itself was not used to support jacks. With a user-oriented design, the guitar input would have been placed at the bottom of the unit, thus leaving free access to the switches.
Plastic enclosures
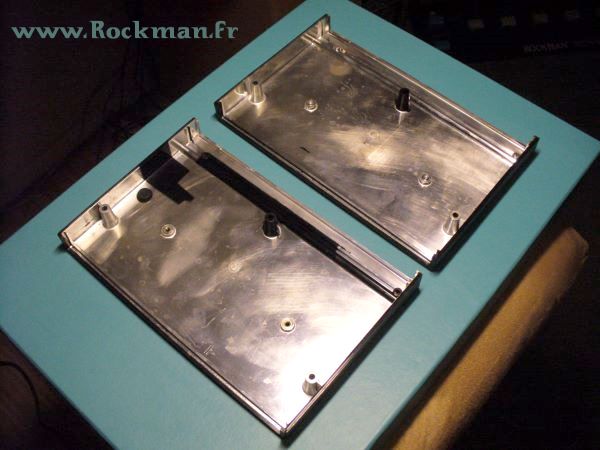 |
Several SR&D items were based on symmetrical plastic parts. They were molded by pairs, and equipped with the proper hardware to become a rear or a front, or a top and a bottom.
- The Power-Soak front and rear panels
- The Headphone Amps half-enclosure
- The Rockadaptor
- The Rockmodules half-enclosure
- The XP100 half shelves
Plastic was chosen every time mechanical and thermal resistance was not strictly necessary: the Rockmodules are the perfect example, since they are supposed to be mounted in a rack that protects them.
Plastic allowed molding a precise shape, but also implied an extra metal sheet to ensure a correct electro-magnetic shielding: we find these metal sheets both in the headphone amps and the Rockmodules.
In some DG's and also some Sustainors, the metal sheets were replaced by shielding paint, as shown on the left.
|
In the Power Soak, the main part (the grill) is made of metal because of the heat dissipation constraint, while the front and rear panels are made of plastic, certainly cheaper than die-cast aluminium: metal would have been, in this case, over-design.
The Headphone Amps plastic enclosure has proved its resistance: 25 years later, they are still here, with only scratches on them. The two parts are strictly identical, and the difference was made by silkscreen writing on the rear part, and an adhesive dual-sheet on the front part. The same principle was used for the Power Soak: the same mould was used for the two panels.
As for the Rockmodules, the top and bottom shells are only almost identical: the bottom part has nuts for the rackmount screws and for the three screws that close the box, while the top part has only three holes for these screws.
The XP100 is a unique concept, still today: it's the only real stereo guitar amp, that can be carried in one piece, or used with separate cabs. The two halves of the XP100 are based on the same plastic shelf, assembled by a smart locking system which is also used as a handle. |
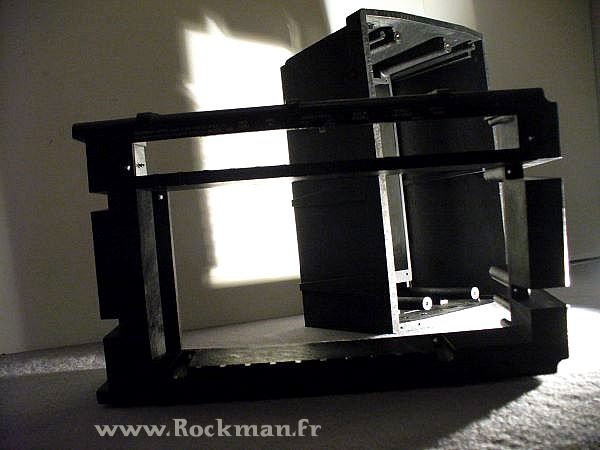 |
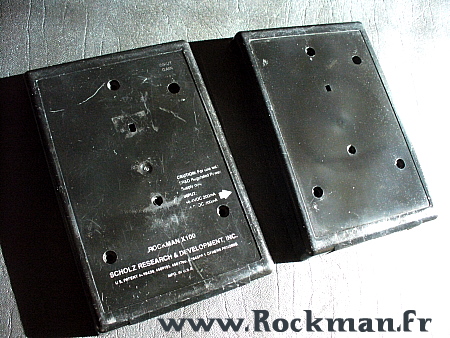 |
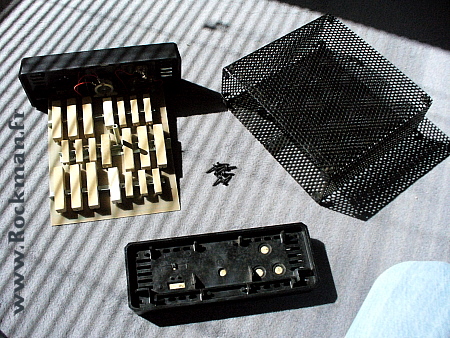 |
Half-rack format
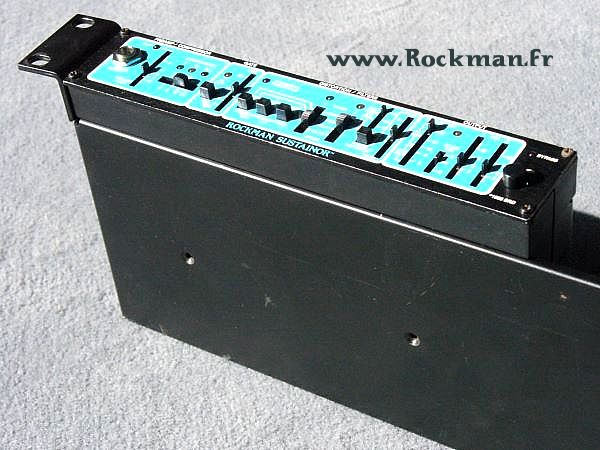 |
While the Rockman headphone amps and the Power Soak enclosures are protected by a patent, the Rockmodule half-rack case was not registered. The design was yet interesting, and can be understood only with the Rackmount, the chassis created to get a standard 19’, 1U ensemble for each pair of modules. Each module is fixed on the Rackmount by two screws. The Rackmount itself was folded to match the groove in the bottom half of the Rockmodules, thus providing correct rigidity and alignment to the assembly.
Inside the Rockmodule, the plastic shapes were designed to receive the rear panel, clamped without screws in the proper slots. All in all, three screws only are necessary to close the box (with the constraint of three holes in the PCB). Then the front plate was fixed with its own small screws: this is the real weakness of the Rockmodules enclosure: the cracked corner syndrome…
All the Rockmodules have the same enclosure, and after the two first modules in 1986 (the Sustainor 100 and the Chorus/Delay), SR&D even managed to have the same rear panel for all of them: eight jack holes were drilled in the metal part, covered by a plastic sheet with the proper number of holes.
|
The Rockmodule principle was and is still unique. The devices were too small for a complete 19’ design, hence the half-rack format. Other manufacturers built and still sell half-rack devices, but SR&D was the only company to propose a complete range of guitar electronic devices in this format.
It was not only logical for a modular system: from a marketing point of view, a musician who starts buying Rockman modules cannot really mix them with other brands gear: he was, in fact “prisoner of the concept”…
|